How do alumina PCBs compare to ceramic substrates?
alumina PCBs compare
With superior high-temperature performance and electrical conductivity, alumina PCBs support a wide variety of demanding applications at power levels unattainable by standard FR-4 boards. Their robust durability and resistance to moisture also make them an excellent choice for medical applications. Properly fabricated alumina PCBs can also deliver exceptional working lifespans and high mean time between failure (MTBF) values. Tight material and dimensional control during production reduce flaws, shorts, open circuits and other common errors to minimize risks of faulty function and early product failure.
The thermal conductivity of alumina pcb ceramics is very efficient, with a low coefficient of thermal expansion (CTE) and high glass transition temperature. This allows heat to dissipate effectively through the substrate, providing superior performance in high-power applications where rapid temperature changes are expected.
Alumina’s crystalline nature also makes it very hard and durable. It has a tensile strength of up to 2 GPa and compression strengths of over 100 MPa. The high-melting point of alumina makes it ideal for sintering into a dense multilayer circuit board.
Website design By BotEap.com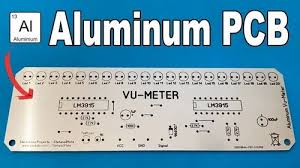
How do alumina PCBs compare to ceramic substrates?
To ensure good electrical insulation, alumina is coated with copper oxide to form the core layer of the circuit board. This layer has a thickness of between 1 and 6 microns. The conductive layers of alumina are then applied by either screen printing or thick film technology. Metallization options include tungsten (W), molybednum-manganese (MoMn) and copper-tungsten (CuW). Conductor traces are then patterned onto the surface of the core layer, and the entire assembly is baked in a furnace at 1000 degC to sinter the conductive layer into the alumina base.
The alumina core layer can be etched with various etching processes. Alumina’s refractory properties also allow it to be etched at higher temperatures than some other types of PCB materials. The resulting conductive layers are then soldered to the other components in the assembly, and the board is ready for operation.
Despite their advantages, there are some things to keep in mind when considering using alumina PCBs in your next project. For one, the high electrical insulation and corrosion resistance of alumina mean that it is not suitable for flexing or folding. This is because it could break the conductive layers that are affixed to the board.
Similarly, alumina is not an alternative for metals like gold, silver and aluminum due to its high melting points. It is, however, safe to use with medical devices, as it is non-toxic and has biocompatibility. This is a major benefit in a number of industries, especially the healthcare sector, where high reliability and safety are paramount. It is also ideal for high-performance consumer electronics and automotive technologies, where the need for small, lightweight and reliable devices is a key driver of innovation. PCBONLINE offers a range of alumina-based products, including multilayer and single-layer alumina circuit boards. To learn more, contact a PCBONLINE sales representative today. Our experts will be happy to help! You can also request a quote online. We look forward to hearing from you!