Variable Frequency Drives – AC motor control system
Variable Frequency Drives
A variable frequency drive (VFD) is an AC motor control system that varies the supply frequency to an AC motor to regulate its speed. VFDs are used in industrial applications such as pumps and conveyors to reduce energy consumption and improve overall equipment performance. VFDs can also increase production and lower maintenance costs by optimizing motor operation to operate at the ideal speed for the application, reducing wear on bearings, gears, motors, and other electrical components.
VFDs are available in a variety of styles and configurations to suit the specific needs of a particular application. Different variable frequency drives utilize different methods for varying the output frequency of an AC motor to control its speed. These variations in control technology and design are what differentiate the various types of drives available on the market.
Website design By BotEap.com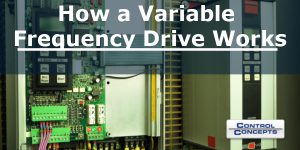
The most common and widely used type of VFD is the pulse width modulation (PWM) drive. The PWM technique varies the input current by switching the inverter power devices – often transistors or insulated-gate bipolar transistors – on and off. By controlling the length of these pulses, the drive can produce a variety of output frequencies and voltages.
Variable Frequency Drives – AC motor control system
Another variation in VFD design is the current source inverter (CSI). A CSI VFD converts the AC input to DC power and uses an inverter device to switch this DC power back to AC. This produces a quasi-sinusoidal AC output that can run a AC induction motor. This VFD is the most popular due to its low cost and ease of setup.
There are also vector control and servo drive technologies that use a microprocessor to compare the actual phase currents and voltages of a given motor with a mathematical adaptive motor model within the drive software to calculate the correct speed, torque, and flux. This algorithm can be used to reduce the harmonics produced by the drive and increase the starting torque of a motor.
A third variation in VFD design is the load-sensing vector control (LSV). In a LSV drive, the actual currents of a given motor are measured using an internal AC transducer and compared to a model generated by the drive software to determine the proper output voltage. The result is a more accurate and stable operation with minimal harmonic generation.
All of these control methods and designs are capable of lowering energy usage by up to 70% in industrial facilities. This allows for greater production capacity, increased product quality, and reduced energy expenses. When combined with energy efficiency tax incentives and utility rebates, returns on investment for a new VFD can be as short as 6 months.